汽车覆盖件及其模具零件型面面积大、造型特征复杂,严重制约模具钳工的研合效率,而模具研合精度直接影响制件的表面成形质量。交付模具周期与覆盖件表面质量已成为主机厂衡量模具企业技术水平的两大重要指标。
随着时代的发展与科学技术的进步,越来越多的计算机模拟辅助软件被应用到模具制造及加工中。通过AutoForm软件模拟成形过程,分析板料在成形过程中各个区域的变薄情况,根据不同区域变薄量来补偿模具零件各区域的偏差间隙,取代传统依靠钳工研合经验来补偿模具零件型面间隙,更加精准地完成模具零件型面各区域的间隙偏差补偿,实现在合模过程中模具闭合时模具型面与制件完全贴合,减少了钳工手工修改模具零件型面的工作量,提升了模具研合效率,实现效率与制件成形质量的双重保证。
汽车模具研合现状
1
模具零件型面的研合精度直接影响外覆盖件的表面成形质量及尺寸精度,故主机厂对模具验收的研合要求也是模具移交的重要指标之一,合资及国产品牌主机厂对重要的模具零件型面要求研合率均要大于95%。
行业的高标准、高要求促使模具制造企业不得不投入更大的人力、物力和财力去提升企业的技术水平,缩短模具的研合工时,减少模具制造成本是提高企业在模具行业中竞争力的重要途径。
表1 覆盖件拉深工序研合标杆工时
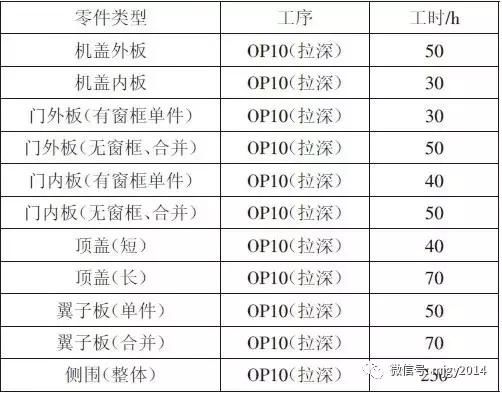
某中日合资模具制造企业给出的各类型车身覆盖件研合所需的标杆工时如表1所示,单工序拉深研合工时长,有较大的提升空间。
影响研合工时原因分析
2
影响模具零件型面的研合工时因素有:
01
模具零件材质,不同的材料在长时间的放置后会发生去应力变形,变形量不一致。
02
数控机床的加工精度,高精度的机床能减小模具零件型面的加工偏差。
03
制件结构,侧围等大型覆盖件的研合工时会大于机盖等。
04
模具在压力机上的受力变形,不同压力机的压力不同,引起的模具零件变形量有较大差异。
05
制件型面的角度差,由于特征造型需要,不同区域与冲压方向形成不同的角度,多角度的存在也增加了研合难度。
06
板料在拉深过程中的变薄,制件各区域的料厚均小于原始厚度且料厚不均等,直接导致模具闭合瞬间板料和模具零件型面不能同时接触,局部区域出现离空现象。
提升模具研合效率的常规对策
3
针对模具零件材质产生的去应力变形而导致模具零件型面研合困难,主机厂和模具制造生产商对模具各部件材质的选用已有自己的参考标准,如表2所示。
表2 模具材质
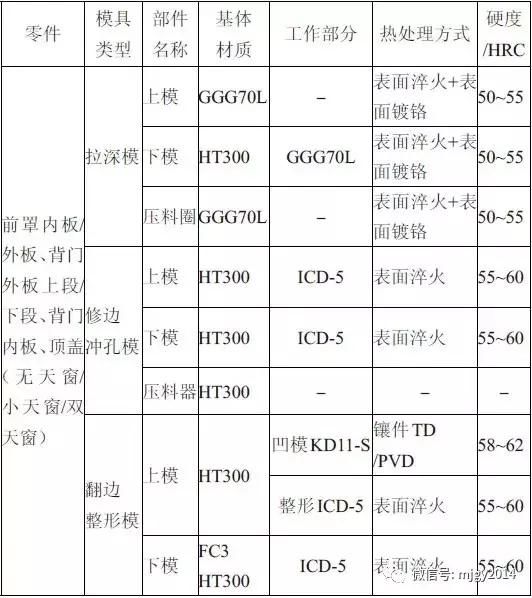
针对模具在压力机上的受力变形而导致模具零件型面产生间隙偏差,许多企业已重视并有了相应的改善措施,通过Jstamp和AutoForm软件分析模具在压力机上的受力变形,将模具零件型面各区域的变形量用阶梯线与数值直观地展示,如图1和图2所示。
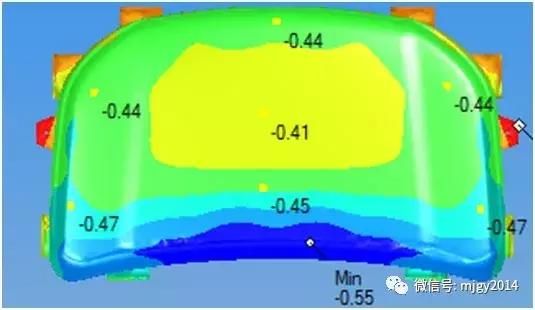
图1 Jstamp计算凸模变形量
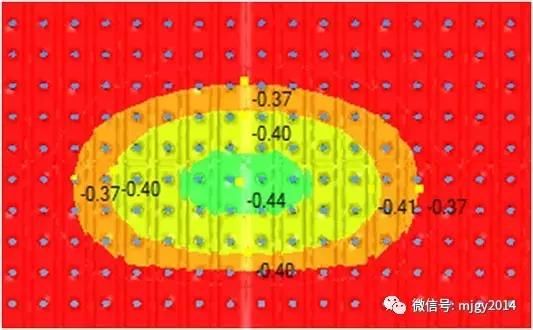
图2 Jstamp计算模具变形量
通过提取模具零件变形阶梯边界线与变形量,采用UG或CATIA软件将变形量补偿到加工数模,消除因模具受力变形而导致的模具零件型面高度差,提升钳工的研合效率,减少钳工的研合工时。
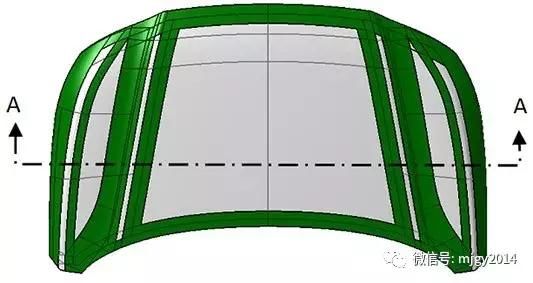
图3 机盖研合要求
针对制件型面角度差导致的研合难度,以某机盖外板为例,黑色部位为要求有研合的型面,灰色部位无研合要求,如图3所示。由于侧壁面及凹成形区域的存在,截面上各区域零件型面的切向角度与冲压方向均存在不同的角度差,如图4所示。
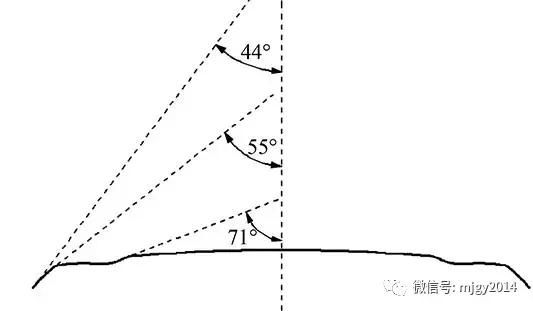
图4 横截面角度差(图3A-A)
制件型面角度差的存在导致在上、下模合模过程中不同角度区域型面间隙存在差异,如图5所示,上模到底前20mm时,侧壁的型面间隙为15.61mm,常规的工艺会结合以往研合经验,根据不同的区域进行相应的强压(零件型面偏差加工)处理(见图6),以减小或消除角度差导致的型面偏差,确保上、下模各区域型面同时接触板料。
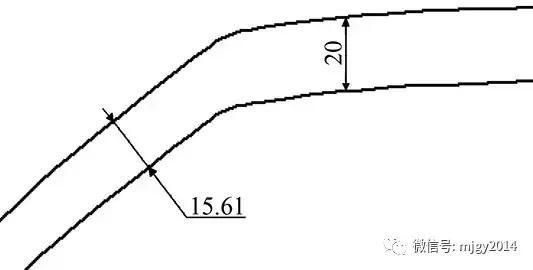
图5上模到底前20mm型面间隙
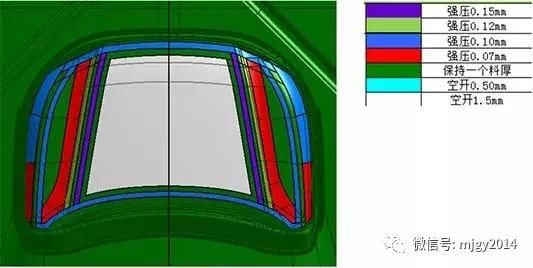
图6 机盖外板强压工艺
但强压工艺有一定的局限性,只考虑型面角度差带来的间隙偏差,并没有考虑板料在拉深过程中变薄而带来的研合间隙偏差,且依靠经验设置强压值并不能解决所有零件的偏差,故该方法不能彻底消除间隙偏差导致的研合困难。
虚拟合模技术的应用
4
现引入虚拟合模的概念,通过AutoForm软件分析板料成形过程中各区域的变薄情况,模拟模具闭合过程,根据板料各区域的变薄量及角度差制定相应的强压工艺,替代依靠经验设置强压工艺,能更加精准控制型面各区域的间隙。
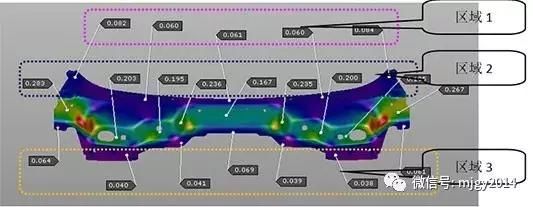
图7 零件成形变薄量
以某汽车搭接件阐述虚拟合模的概念及应用,第一步采用AutoForm分析板料在成形过程中的各区域变薄量t,如图7所示,制件变薄梯度主要分3个区域,区域1板料变薄量约0.06mm、区域2侧壁板料变薄量约0.16~0.28mm、区域3法兰边板料变薄量约0.04mm。
第二步以区域1的板料变薄量作为参考基准值η,拟定在区域1对应的上模零件型面进行η=0.06mm的强压补偿,采用AutoForm软件模拟上模闭合到底前0.06mm时各区域模具零件型面的间隙离空值h,用GOMinspect软件将其呈现,如图8所示。
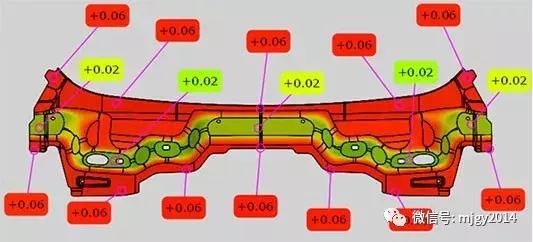
图8 模拟上模到底前0.06 mm各区域模具型面间隙
上模到底前0.06mm时,区域1与区域3的模具零件型面间隙离空值为0.06mm,由于角度差的存在,区域2侧壁零件型面离空值为0.02mm。由此可知,在不考虑板料变薄时,当区域1与区域3进行0.06mm的强压时,区域2侧壁只需要进行η-0.02mm=0.04mm的强压即可满足各区域制件同时接触模具零件型面。当考虑板料变薄因素时,得出强压设置公式θ=-t+η-h来满足各区域型面的间隙要求。
区域1最终的强压值:θ=-0.06+0.06-0.06=-0.06mm
区域2最终的强压值:θ=-(0.16~0.28)+0.06-0.02=-(0.12~0.24)mm
区域3最终强压值:θ=-0.04+0.06-0.06=-0.04mm
其中,θ为上模零件型面所需的强压量;t为板料成形后的变薄量;h为在初始参考基准值下上、下模零件型面的离空数值;负号表示强压是向下模侧置补偿。
第三步通过UG或者CATIA软件将各区域强压量补偿到加工数模,完成补偿的加工数模各区域型面的强压值如图9所示。
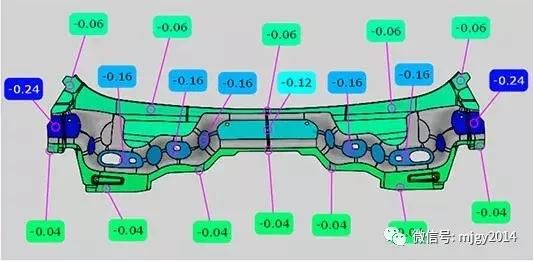
图9 型面偏差加工强压值
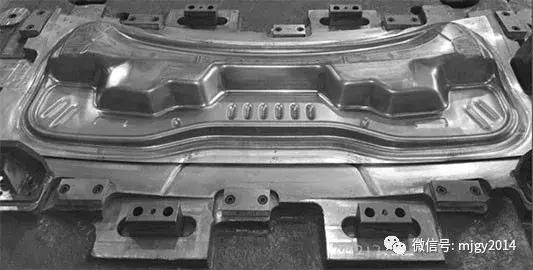
图10 现场实际研合效果
该制件运用虚拟合模技术后的研合效果如图10所示,拉深模在研合8h后模具零件型面研合率已达到90%以上,成功缩短研合工时,提高了研合效率。